Sectional warping is preferred over beam warping for multi-coloured warp. Here the entire width of the warping drum is not developed simultaneously. It is developed section by section as depicted in Figure 3.6. As only one section is built at a time, a support is needed at one side of the drum. This is provided by making one side of the drum inclined. The inclination can be of two types.
|
- Fixed angle
- Variable angle (7 0, 9 0, 11 0 etc.)
|
As the winding of one layer is completed on the drum, the section of ends is given a requisite traverse so that the end at one extreme corner touches the inclined surface. Thus it gets support from the inclined surface.
|
|
Figure 3.6: Schematic representation of sectional warping principle
|
As the process continues, the thickness (or height) of the section gradually increases. When requisite length has been wound in a section, next section is started by shifting the expandable reed assembly by suitable distance (distance s of Figure 3.7)
|
|
Figure 3.7: Traverse in sectional warping |
If α is the angle of inclination, x is the traverse given to the section and h is the height of the section then
|
|
For drum with fixed angle, if the yarn is coarser then one layer of the warp ribbon will result in higher increase in thickness (Δh) and thus to match the inclination, the traverse speed (Δx) should be higher. The machines are designed with provisions to change the traverse speed so that a wide range of yarn counts can be managed. For fixed angle drums, only one variable i.e. traverse speed is to be adjusted while with variable angle drums both traverse and the angle of inclination can be varied.
|
For drums with variable angle, the angle is changed by changing the inclination of metal plates which are supported at the end of the drum. When the angle is increased, larger gaps are created between the neighboring metal plates. Therefore, the yarn will remain unsupported at the gaps between two metal plates.
|
The flow chart of the warping process can be represented as shown in Figure 3.8.
|
|
Figure 3.8: Sequence of warping process |
Leasing: It is asystem by which the position of the ends is maintained in the warp sheet. Generally it is done by dividing the ends in two groups (odd and even). If odd ends are passing over the lease rods then the even ends will pass below the rod. The relative positions of the ends will reverse in case of second lease rod.
|
Expandable reed: It is used to control the spacing between consecutive ends. The two limbs of V shaped expandable reed can be expanded or collapsed as per the required spacing of ends. Figure 3.9 shows the expandable reed and lease rods in a sectional warping machine.
|
Beaming system: In the beaming process, all the sections are simultaneously transferred to the flanged warper’s beam (Figure 3.10). The drum is rotated by the tension of warp sheet whereas positive drives are given to the warper’s beam. The speed of beaming process in sectional warping is quite slow (around 300 m/min).
|
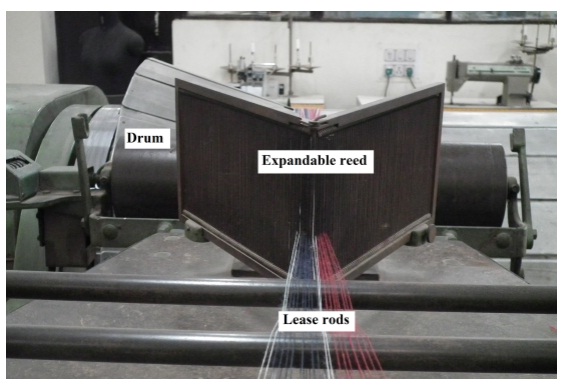
|
Figure 3.9: Expandable reed and lease rods |
|
Figure 3.10: Sectional warping drum and beam
[Courtesy: Prashant Group, www.prashantgroup.com/swm_sbeam.htm ] |
Table 3.1 presents the comparison between beam warping and sectional warping |
Table 3.1: Comparison between beam warping and sectional warping |
Beam warping |
Sectional warping |
Used for high volume production |
Used for small volume and customised production (stripes and specialised yarns) |
One step process |
Two step process |
High creel capacity is required |
Low creel capacity is sufficient |
Comparatively less expensive |
Comparatively more expensive |
Beaming speed is high |
Beaming speed is low |
More common |
Less common |
|
|
|